Electrical control panels (EC powercon) are crucial elements within automated equipment, comprising various electrical devices that manage power distribution to regulate the mechanical functions of industrial machinery. However, many facilities install them and then overlook their maintenance, which can pose significant risks and lead to unnecessary expenses. Upgrading an aging control panel with a modernized version not only enhances facility safety but also promises improvements in productivity, efficiency, and reliability. These advancements in control panel technology are poised to streamline operations, potentially reducing production costs associated with outdated electrical devices that could be hindering optimal performance.
Table of Contents
What Function Does an Electrical Control Panel Serve?
While the specifics of control panel elements and operations differ based on the machinery or process they oversee, essentially, electrical control panels manage power distribution, oversee operations, and safeguard equipment. A basic electrical control panel receives power from a source and disperses it to components like circuit breakers and power relays, crucial for equipment functionality. However, with technological advancements, contemporary electrical control panels boast enhanced intelligence compared to older models. Upgrading from outdated control panels to modern ones not only enhances safety but also yields substantial financial advantages. This article will elucidate when it becomes imperative to replace an aging control panel and how new technologies can curtail production expenses.
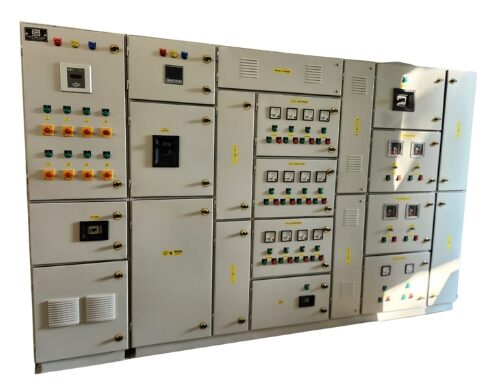
When to Replace an Aging Electrical Control Panel
Here are five clear indications that an electrical control panel poses a safety concern and necessitates replacement:
- Frequent tripping of circuit breakers: This suggests aging or malfunctioning circuit breakers, deteriorating insulation on conductors, or equipment overload, all of which can pose serious electrical hazards.
- Presence of frayed or damaged wires, loose connections, or exposed live parts: These conditions present significant safety risks and can lead to fires or electrical accidents.
- Visible signs of rust, water damage, or an inability to properly close the panel door: Since water and electricity are a dangerous combination, it’s crucial to rectify water damage sources promptly and replace compromised electrical components and panels to avert potential disasters.
- Detectable burning odors, sparking during plug insertion, or buzzing noises emanating from the breaker box: These symptoms signal serious issues within the control panel, such as overloaded circuits, wiring shorts, faulty breakers, or equipment malfunctions, demanding immediate attention to prevent major hazards.
- Obsolete components: If certain parts are becoming scarce or discontinued, it may be necessary to replace the panel to ensure timely availability of components.
- Installation of New Equipment: Upgrading or replacing equipment may require a higher power supply than what the current control panel can provide. In such cases, a service upgrade is essential to safely meet the voltage and power requirements of modern equipment. Moreover, newer automated systems may offer enhanced features that can be accommodated by an advanced control panel with improved technological controls. Embracing these developments and upgrading control mechanisms can offer various production-related benefits.
The Advantages of Using Modern Electrical Control Panels
The primary aim of electrical control panels (EC powercon) is to safeguard, consolidate, and arrange electrical parts. However, contemporary control panels now incorporate state-of-the-art components and technologies to enhance the efficiency of powering and managing electrical and automated machinery. This integration offers several benefits:
Advantages | Description | Example |
---|---|---|
Enhanced Process Control | Updated panels offer modern controls in a centralized area, simplifying operation and enabling quick emergency shutdowns. | Centralized control location in modern panels allows operators to swiftly manage equipment, enhancing safety and efficiency. |
Increased Efficiency and Optimization | Customizable panels facilitate monitoring and adjustment of process variables for optimal machine performance. Real-time data collection enables operators to maintain equipment within specifications, enhancing process conditions. | PLCs and other hardware in panels collect data to determine equipment performance, aiding operators in taking corrective actions for optimized processes. |
Reduced Downtime | Panels can predict and identify equipment issues, alerting operators and maintenance staff for timely repairs. Proactive maintenance scheduling reduces unscheduled downtime, increasing equipment uptime and productivity. | Predictive maintenance capabilities in panels minimize breakdowns, maximizing equipment and facility uptime for enhanced productivity. |
Increased Product Quality | Centralized control reduces human error in automated systems, ensuring consistency and reliability. This leads to improved product quality and reduced waste or re-work. | Greater precision in controlling automated systems via centralized panels minimizes inconsistencies between operators, enhancing product quality. |
Increased Energy Efficiency | Real-time data from panels identifies power disruptions, facilitating quick adjustments for optimal equipment performance. Advanced technology reduces electricity bills by boosting electrical reliability and efficiency. | Advanced panels provide insights on power system disruptions, enabling operators to optimize equipment for increased energy efficiency and reduced costs. |
For further details on upgrading your electrical control panels and enhancing facility safety and efficiency, reach out to EC3 Powercon.